Antecedentes: Para una prueba en QUV podemos elegir entre dos condiciones que dan la misma cantidad de energía total:
Prueba A: 0.65W/m2 irradiación durante un tiempo de 3000 horas.
Prueba B: 0.83W/m2 irradiación para 2500h.
Las muestras de prueba son las películas, con un espesor entre 80 y 100 micras. Al final de la prueba de cada uno, se verifica el cambio de color en escala de grises y retener la propiedad mecánica.
¿Podemos comparar los dos resultados?
Respuesta: Es común suponer que las dos exposiciones son los mismos, pero en muchos casos los dos se producen diferentes resultados. Existen sinergias complejas entre la irradiancia, el calor y la humedad. En general, cuando esta pregunta se estudia, hay una diferencia mucho mayor entre puntos de ajuste de irradiancia. La cuestión es así: si se duplica la irradiación de la exposición, se puede reducir el tiempo de prueba a la mitad y lograr los mismos resultados?
Algunas veces hay una relación lineal entre la irradiancia y la velocidad de degradación, pero a veces no. En el ejemplo de la cuestión, la diferencia es pequeña, por lo que existe una mayor probabilidad de que los resultados son comparables.
Aún así, me gustaría llevar a cabo su propio estudio y averiguar. Estaría interesado en aprender de sus resultados.
La uniformidad de irradiación de la cámara de intemperismo acelerado QUV es excelente: más del 90% sobre el área de exposición de la muestra.
La uniformidad de irradiación puede caer en el borde de la cámara debido a las limitaciones físicas y geométricas que se aplican a todos las cámaras de fluorescencia UV. Por esta razón, Q-Lab sugiere la reposición regular de muestras. Esta práctica mejora también el spray de agua y la uniformidad de la temperatura en la intemperie acelerada y en los equipos de corrosión.
Con una instalación y un montaje de muestras adecuados, la uniformidad de la temperatura en el QUV también es muy buena. Sin embargo, es muy importante que evite dejar brechas en los extremos o entre las muestras. Estos huecos hacen que el aire salga de la cámara, lo que provoca el enfriamiento en muestras adyacentes y causa puntos calientes en otros lugares.
Las normas internacionales para la operación de aparatos de prueba de intemperismo que utilizan lámparas de luz fluorescente UV y de arco de xenón a menudo incluyen requisitos para las Distribuciones de Potencia Espectral relativa (SPD por sus siglas en inglés) de las fuentes de luz. Estos SPD definen los rangos para los porcentajes de irradiación de una fuente de luz dada dentro de un paso de banda específico, por ejemplo 290-320 nm o 360-400 nm.
Conjuntos importantes de tablas de referencia de SPD se proporcionan en las normas ASTM e ISO. Las tablas espectrales de UV fluorescentes se proporcionan en ASTM G154 e ISO 4892-3, mientras que los requisitos de arco de xenón se encuentran en ASTM G155 e ISO 4892-2. Estas tablas se definen para tres clasificaciones generales de lámparas y filtros: Luz diurna (luz solar exterior), Ventana (detrás de un vidrio) y UV extendido (UVB-313).
Las lámparas UVA-340, UVA-351 y UVB-313EL de Q-Lab cumplen todas las especificaciones de ASTM G154 e ISO 4892-3 para luz diurna, ventana y UV extendido.
Los siguientes filtros UV de Q-Lab utilizados en los equipos de intemperismo Q-SUN cumplen con los requisitos espectrales especificados en ASTM G155 e ISO 4892-2. La última norma no incluye una especificación para UV-extendido.
Tabla 1 (Filtros de luz diurna): Daylight-B/B, Daylight-Q, Daylight-F
Tabla 2 (Filtros de vidrio de ventana): Window-B/SL, Window-Q, Window-IR
Tabla 3 (Filtros UV extendidos): Extended UV-Q/B
Los únicos filtros ópticos estándar de Q-Lab que quedan fuera de estos requisitos de SPD son los filtros UV-Quartz extendido y Window-SF5. El filtro UV-Quartz extendido se requiere solo en pocas normas aeroespaciales especializadas, mientras que el filtro Window-SF5 se usa solo en normas automotrices que especifican vidrio con longitudes de onda más altas que el vidrio arquitectónico.
Las pruebas al exterior automotrices han estado utilizando el spray posterior (back spray) durante años. Este se requiere para correr SAE J2527, el reemplazo basado en el rendimiento para SAE J1960. Esta es la única norma que conocemos que requiere esta singular función. Aunque sí ofrecemos una opción de spray posterior (back spray) en nuestros equipos Q SUN Xe-3 y Xe-2 para cumplir con esta norma, uno todavía puede preguntarse: ¿la función de spray posterior (back spray) logra algo? ¿Es útil?
La respuesta a ambas preguntas es un NO inequívoco. Además, el spray de agua posterior más que favorable es contraproducente, ya que desperdicia mucha agua y puede a veces incluso lavar las etiquetas de las muestras.
El requisito de spray de agua posterior en SAE J2527 proporciona un buen ejemplo de los peligros de las normas de intemperismo basados en hardware. El equipo original utilizado en el desarrollo de este estándar se configuró incorrectamente para esta "característica" de spray de agua posterior hace más de 25 años, y su implementación a través de un estándar basado en hardware obligó a todos a propagar este error. Como resultado, hoy nos encontramos con un estándar que usa más del doble del agua que debería, solo se puede ejecutar en ciertos equipos y no produce mejores resultados que los procedimientos de prueba de spray de agua frontal.
En las pruebas de intemperismo acelerado, el agua es a menudo el factor más difícil de acelerar. No se puede hacer que el agua se siente en un panel "más rápido" en un equipo que en el mundo real. Dado que muchos materiales al aire libre estarán húmedos durante 8 a 12 horas al día, en muchos casos una prueba acelerada debe simular la misma penetración profunda del agua en el material para correlacionarlo con las condiciones del mundo real, y esto significa que debe estar húmedo por mucho tiempo.
Una forma en que podemos acelerar los efectos del agua es aumentando la temperatura del agua. A medida que aumenta la temperatura, el aire puede contener más vapor de agua, lo que permite una mayor absorción de agua en los materiales. Dado que la condensación se forma a partir de vapor de agua caliente, la temperatura del agua se controla fácilmente y la cámara puede alcanzar temperaturas de hasta 60°C. En contraste, es difícil ejecutar una etapa de rociado de agua en un equipo de luz de arco de Xenón o fluorescente de luz UV mientras se mantienen simultáneamente altas temperaturas de la muestra, por lo que la captación de agua es más difícil con el spray de agua que con la condensación.
Pero, ¿cómo "mojado" es un paso de condensación?
Es difícil apreciar realmente cuán húmedo es un paso de condensación porque es menos obvio que mirar el spray de agua. La Figura 1 muestra un conjunto de siete imágenes que muestran cuán húmeda está la primera hora de un paso de condensación.
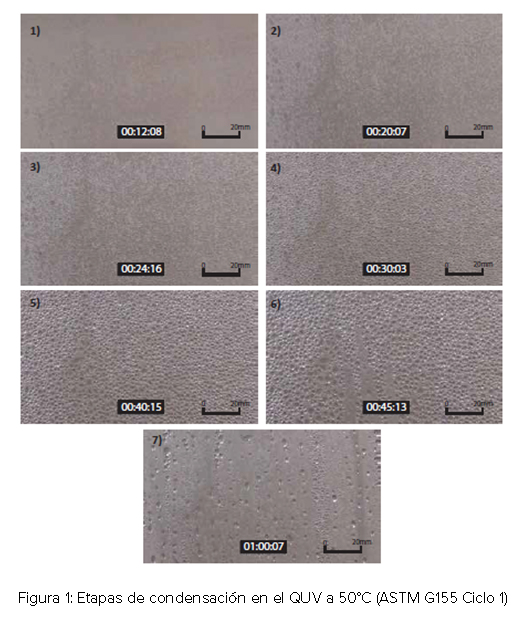
Una vez que todas las gotas iniciales se han presentado en la muestra, el ciclo se repite con la formación de gotas pequeñas, las gotas se hacen más grandes y las gotas grandes se salen de la muestra. En cualquier momento del ciclo de condensación de 20 minutos o más, las muestras se cubren con agua y, en el transcurso de cuatro horas, la condensación se forma y gotean continuamente de las muestras.
La mayoría de las personas esperarían que las muestras de prueba de intemperismo en un paso de condensación QUV estén expuestas a solo una pequeña cantidad de agua. En realidad, a lo largo de cuatro horas, una etapa de condensación no solo proporciona una exposición casi continua al agua, sino que también eleva la temperatura del aire saturado, exponiendo una muestra a una mayor cantidad de vapor de agua. A menos que esté probando un material grueso y aislado, la condensación en caliente en un equipo QUV es la mejor manera de acelerar la absorción de agua en una prueba de intemperismo.
Las normas de prueba de intemperismo y resistencia a la luz típicamente especifican un nivel de irradiación como una magnitud y la longitud de onda (o rango de longitud de onda) donde se controla. La irradiación en los medidores de intemperie de rayos UV y de arco de xenón se puede controlar mediante el uso de valores de banda angosta o puntos de banda ancha.
La selección de un punto de control de banda estrecha en un equipo de UV fluorescente QUV está determinada por el tipo de lámpara UV en uso. Para un equipo de intemperie de arco de xenón Q-SUN, sugerimos control usando una región de longitud de onda o de longitud de onda en la que la muestra de prueba sea sensible. Si el usuario está preocupado principalmente por el cambio de color, a menudo se usa un punto de control de 420 nm. Si el área principal de preocupación es otro tipo de cambio de propiedad física, por ejemplo, la pérdida de brillo, se usa con frecuencia un punto de control de 340 nm. Un punto de control TUV de banda ancha (300-400 nm) puede verse como un compromiso entre los dos puntos de control de banda estrecha (340 nm y 420 nm), ya que utiliza la irradiación total en el rango de 300-400 nm como su punto de ajuste.
La selección de filtros ópticos en un medidor de arco de xenón también suele ser paralela a esta selección de punto de control de irradiación. Por lo general, los usuarios que realizan pruebas con filtros ópticos de luz diurna usan un punto de control de 340 nm, mientras que los usuarios de filtros ópticos de vidrio de ventana generalmente usan un punto de control de 420 nm. Las selecciones disponibles y más comunes para cada tipo de lámpara o filtro se presentan en la Tabla 1.
Las lámparas QFS-40 y UVB-313EL ambas se usan en equipos de intemperismo acelerado QUV para proporcionar luz UV fluorescente que incluye un componente UVB significativo para pruebas más rápidas. El siguiente diagrama muestra que ambas tienen distribuciones de potencia espectral de forma similar. ¿En qué se diferencian estas lámparas y cuál es la mejor para usar en su QUV?
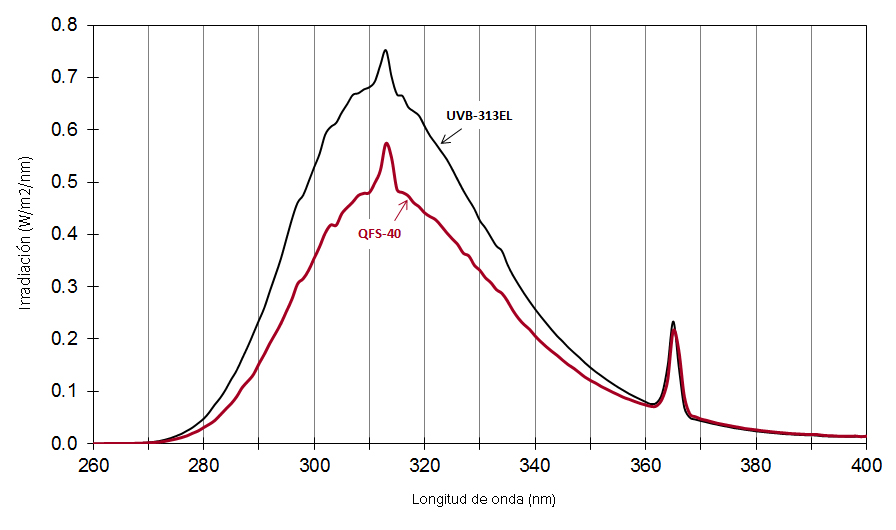
La lámpara QFS-40 fue desarrollada para cumplir con las especificaciones de SAE J2020, que una vez escrita, tenía un requisito específico de hardware para usar esta lámpara. Ese requisito específico de hardware se ha eliminado en SAE J2020 y en la mayoría de las normas que se basan en SAE J2020.
Las lámparas UVB-313EL se desarrollaron más adelante y funcionan con el sistema de control de irradiación SOLAR EYE de QUV para proporcionar un nivel de irradiación más consistente y repetible que el uso de las lámparas QFS-40 en un QUV/básico, debido al envejecimiento de la lámpara, el mantenimiento y las condiciones ambientales. Las lámparas UVB-313EL son significativamente menos costosas que las lámparas QFS40, porque se fabrican volúmenes mucho mayores de UBV-313EL.
Si su QUV tiene control de irradiación SOLAR EYE, debe usar lámparas UVB-313EL y configurar la irradiación a 0.48 W/m2 a 310 nm para SAE J2020 y normas basados en él, incluso si estas normas no se han actualizado para incluir la lámpara UVB-313. Esta es la opción más rentable y de mejor desempeño cuando el control de irradiación está disponible. Si su QUV no tiene control de irradiación (modelos QUV/básicos o de estilo antiguo), debe continuar usando las lámparas QFS-40 para mantener niveles de irradiación comparables a los que se pretende en un estándar de prueba o práctica histórica. Las lámparas UVB - 313EL utilizadas en los equipos de QUV sin control de irradiación generarán una irradiación que es significativamente mayor que las lámparas QFS-40 en el mismo equipo.
En los ensayos de envejecimiento de arco de xenón y fluorescencia UV un valor de setpoint no es información suficiente sin una referencia de longitud de onda o un rango de la longitud de onda que representa. Existen dos clases de setpoints de irradiancia.
Banda estrecha: Estos setpoints incluyen longitudes de onda de 340 nm y 420 nm, y representan un paso de banda de 1nm de ancho centrado en el valor de longitud de onda indicado (por ejemplo, puede estar a ½ nm a cada lado de 340 nm). Las irradiancias en banda estrecha se expresan con unidades de “Vatios por metro cuadrado por nanómetro”. Este se puede escribir como W/ (m2.nm), W/m2/nm o w.m-2.nm-1.
Banda Ancha: Estos setpoints (Usualmente conocidos como “TUV” o “UV total”) son la integración de la irradiancia de todas las longitudes de onda entre los dos longitudes de onda definidas, comúnmente se usan 300-400 nm (Acelerado en laboratorio) o 295-385 nm (exterior). Como resultado, los valores de irradiancia en banda ancha son mucho más grandes que los valores de irradiancia de banda estrecha. La irradiancia en banda ancha se mide “Vatios por metro cuadrado”, se puede expresar como W/m2 o W.m-2.
El gráfico en la parte inferior es el poder de distribución del espectro (SPD por sus siglas en inglés), representa la irradiancia en función de la longitud de onda. Este SPD muestra que para esta fuente de luz en particular se puede describir la irradiancia como de banda estrecha a 0.35 W/m2/nm @340 nm o como una irradiancia de banda ancha de 40 W/m2 desde 300 – 400 nm (TUV).
The water pan in a QUV tester is made from stainless steel, and in most cases does not experience corrosion. To deal with those rare cases where a QUV water pan does corrode, Q-Lab offers a “Super Alloy” QUV water pan that is more corrosion-resistant than stainless steel.
This Super Alloy water pan is not intended for cases where the observed corrosion or oxidation is actually only non-corrosion debris, as in the photo below. This buildup of precipitated minerals over time may occur when tap water is used in a QUV SE or Basic testers (DI water is required for Spray models). Although tap water is acceptable for use in a non-spray QUV, its use does requires more frequent cleaning of the water pan. If you see debris buildup like this in your QUV, you may have “hard water” and should consider the use of reverse osmosis/deinoized (RO/DI) purified water with your QUV.
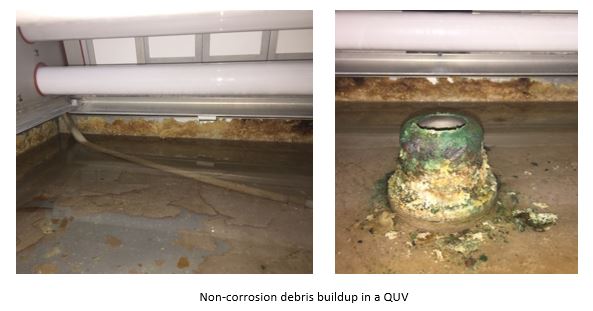
However, in some cases, actual corrosion of the stainless steel water pan is observed, as in the photo below. Replacing your stainless steel QUV water pan with a Super Alloy water pan is appropriate to correct this problem. Furthermore, if corrosion like this is observed in one QUV, a Super Alloy water pan should be installed in all other QUV’s located in the same laboratory as the corroded QUV.
La bandeja de agua en un equipo QUV está hecha de acero inoxidable, y en la mayoría de los casos no experimenta corrosión. Para lidiar con los casos raros en que una bandeja de agua para QUV se corroe, Q-Lab ofrece una bandeja de agua para QUV de "Super Aleación" que es más resistente a la corrosión que el acero inoxidable.
Esta bandeja de agua de super aleación no está diseñada para los casos en los que la corrosión u oxidación observada es en realidad solo residuos no corrosivos, como se muestra en la foto de abajo. Esta acumulación de minerales precipitados a lo largo del tiempo puede ocurrir cuando se utiliza agua del grifo en los equipos QUV SE o Basic (para los modelos de spray se requiere agua DI). A pesar de que el agua del grifo es aceptable para su uso en un QUV sin spray, su uso requiere una limpieza más frecuente de la bandeja de agua. Si observa una acumulación de desechos como esta en su QUV, puede tener “agua dura” y debe considerar el uso de agua purificada por ósmosis inversa / desionizada (RO/DI) con su QUV.
Sin embargo, en algunos casos, se observa la corrosión real de la bandeja de agua de acero inoxidable, como en la foto de abajo. Reemplazar su bandeja de agua QUV de acero inoxidable con una bandeja de agua super aleación es apropiado para corregir este problema. Además, si se observa una corrosión como esta en un QUV, se debe instalar una bandeja de agua de super aleación en todos los otros QUV ubicados en el mismo laboratorio que el QUV corroído.
Los equipos de corrosión e intemperismo acelerados de Q-Lab tienen algunos métodos para medir y controlar la temperatura, incluidos los termómetros de panel negro (BPT) y los sensores de temperatura del aire de la cámara (CAT). Los resultados confiables de las pruebas dependen de la calibración precisa de estos dispositivos.
Muchos de los sensores que miden y controlan la temperatura en los equipos de intemperismo y corrosión Q-Lab se pueden calibrar utilizando un termómetro de referencia estándar y un recipiente de agua aislado. Estos dispositivos incluyen:
- Sensores de temperatura del aire de la cámara (CAT) en el Q-FOG, QCT y (opcionalmente) el Q-SUN Xe-1
- Termómetro de panel negro (BP) en el QUV
- Termómetro BP durante la prueba de inmersión en caliente.
- Termómetros de bulbo húmedo / bulbo seco en el Q-FOG CRH
Sin embargo, los termómetros de referencia estándar no se pueden usar para calibrar la temperatura de un panel negro sin aislamiento (BP, también conocido como panel negro) o panel negro aislado (IBP, también conocido como estándar negro) utilizado en un equipo de arco de xenón Q-SUN porque reciben principalmente su calor al absorber la energía radiante de la luz ultravioleta (UV), visible e infrarroja (IR) y pierden calor a través de la convección al aire de la cámara. Por lo tanto y como resultado, para ser calibrado correctamente, un Q-SUN BP o IBP debe compararse con un termómetro de calibración especial, un UC202 o CT202, que es en sí mismo un sensor de panel negro que ha sido calibrado para incluir los efectos del calor radiante y enfriamiento por convección del aire. Esto no es necesario para los sensores descritos en la sección anterior porque los sensores de aire de la cámara y los termómetros de bulbo húmedo/seco no están expuestos a ningún calor radiante proveniente de fuentes de luz.
Los probadores de intemperismo acelerado QUV y Q-SUN requieren el uso de radiómetros de calibración especiales. Las lámparas CR10 y UC10 se usan para lámparas UV fluorescentes y las lámparas CR20 y UC20 para lámparas de xenón. Estos dispositivos rastreables por NIST aseguran que la irradiación entregada a las muestras de prueba sea igual a la irradiación requerida en el método de prueba del usuario. Las lámparas de Q-Lab deben calibrarse específicamente con este equipo de radiometría debido al desajuste espectral entre las fuentes de luz.
Los sensores de irradiación a bordo y de calibración de Q-Lab funcionan con un fotodiodo, un semiconductor que convierte los fotones absorbidos en una corriente eléctrica. La sensibilidad de estos fotodiodos varía según la longitud de onda. Sin embargo, la salida eléctrica no proporciona información sobre a qué longitudes de onda proviene la energía, por lo que los dispositivos de calibración no pueden diferenciar, por ejemplo, la energía de los fotones a 350 nm y a 300 nm, a pesar del hecho de que la irradiación a 350 nm crea una Salida de potencia eléctrica más alta del fotodiodo que la irradiación equivalente a 300 nm. Es por esto que es crítico calibrar el UC10 específicamente con lámparas QUV y el UC20 específicamente con las lámparas de xenón con el filtro óptico correcto. La curva espectral de la irradiancia observada por el fotodiodo debe tenerse en cuenta para producir una medición precisa.
Un factor de conversión determinado para una lámpara UVA-340 solo se aplica a ese tipo de lámpara. La medición de cualquier otra fuente de luz UV, como la luz solar o una lámpara UVB-313, usaría un factor de conversión incorrecto. Cuando se seleccionan las lámparas UVA-340 o UVB-313 en la pantalla UC1, se le indica al sistema UC que tenga en cuenta las curvas espectrales UVB-313 al convertir la corriente eléctrica en una irradiación. El uso de un factor de conversión para una fuente de luz diferente proporciona una calibración inexacta, lo que se conoce como error de falta de coincidencia espectral.
Un factor de conversión determinado para una lámpara UVA-340 solo se aplica a ese tipo de lámpara. La medición de cualquier otra fuente de luz UV, como la luz solar o una lámpara UVB-313, usaría un factor de conversión incorrecto. Cuando se seleccionan las lámparas UVA-340 o UVB-313 en la pantalla UC1, se le indica al sistema UC que tenga en cuenta las curvas espectrales UVB-313 al convertir la corriente eléctrica en una irradiación. El uso de un factor de conversión para una fuente de luz diferente proporciona una calibración inexacta, lo que se conoce como error de falta de coincidencia espectral.
La Legionella o legionelosis es un grupo de bacterias que pueden causar una enfermedad tipo neumonía llamada enfermedad de los legionarios y una enfermedad leve parecida a la gripe llamada fiebre de Pontiac. La Legionella o legionelosis puede crecer en trampas de drenaje, bandejas de agua, depósitos y torres de enfriamiento comerciales e industriales. Aunque los evaluadores de QUV y QCT de Q-Lab tienen condiciones cálidas y húmedas que podrían ser propicias para el crecimiento de microorganismos, no se han reportado casos de enfermedad del legionario relacionado con el uso de QUV y QCT durante más de 45 años y millones de horas de operación de campo. Esto se debe en gran parte a que el QUV y el QCT generalmente se ejecutan a temperaturas que matan a la bacteria Legionella.
El mejor medio de prevención es realizar un mantenimiento básico que evite las condiciones del agua que permiten que los microorganismos crezcan a niveles altos. Esto incluye:
- Drenaje de agua de probadores no utilizados.
- Realizar el mantenimiento y limpieza regular de las torres de refrigeración y condensadores evaporativos.
- Desinfección con una solución de lejía suave.
- Mantenimiento de calentadores de agua a 60 ° C (140 ° F)
- Evitar las condiciones que permiten que el agua se estanque al proteger los tanques de agua de la luz solar, drenar y enjuagar las líneas de agua no utilizadas.
- Mantener todas las líneas de agua cortas y mantener el flujo. Se han reportado cero casos de enfermedad Legionella o Legionelosis relacionados con el uso de QUV y QCT durante más de 45 años y millones de horas de operación de campo. El mantenimiento adecuado de los probadores Q-Lab es la mejor manera de reducir el riesgo ya minúsculo de Legionella.