Background: For a test in QUV we can choose between two conditions that give the same amount of total energy:
Test A: Irradiance 0.65W/m2 for a time of 3000h.
Test B: Irradiance 0.83W/m2 for 2500h.
The testing samples are films, with a thickness between 80 and 100 micron. At the end of the each test, we verify the change of color in grey scale and the mechanical property retain.
Can we compare the two results?
Answer: It is common to assume that the two exposures are the same, but in many cases the two would yield different results. There are complex synergies between irradiance, heat, and moisture. Generally, when this question is studied, there is a much bigger difference between irradiance setpoints. The question is something like this: if you double the irradiance of the exposure, can you cut the test time in half and achieve the same results?
Sometimes there is a linear relationship between irradiance and speed of degradation, but sometimes not. In the example in the question, the difference is small, so there is greater likelihood that the results are comparable.
Still, I would conduct your own study and find out. I would be interested in learning of your results.
To read more about Q-Lab and to find more articles like this, please visit Q-Lab Blog.
QFS-40 and UVB-313EL lamps are both used in QUV accelerated weathering testers to provide fluorescent UV light that includes a significant UVB component for faster testing. The diagram below shows that both have similarly-shaped spectral power distributions. How do these lamps differ, and which one is best for use in your QUV?
The QFS-40 lamp was developed to meet the specifications of SAE J2020, which, when written, had a hardware-specific requirement to use this lamp. That hardware-specific requirement has been removed in SAE J2020 and in most standards that are based on SAE J2020.
UVB-313EL lamps were developed later, and operate with the QUV’s SOLAR EYE irradiance control system to provide a more consistent and repeatable level of irradiance than using QFS-40 lamps in a QUV/basic, due to lamp aging, maintenance, and environmental conditions. UVB-313EL lamps are significantly less expensive than QFS40 lamps because far greater volumes of UBV-313EL are manufactured.
If your QUV has SOLAR EYE irradiance control, you should use UVB-313EL lamps and set the irradiance to 0.48 W/m2 at 310 nm for SAE J2020 and standards based on it, even if those standards have not been updated to include the UVB-313 lamp. This is the most cost-effective and best-performing option when irradiance control is available.
If your QUV does not have irradiance control (QUV/basic or old style models), you should continue to use QFS-40 lamps to maintain comparable irradiance levels to what is intended by a test standard or historical practice. UVB‑313EL lamps used in QUV testers without irradiance control will generate irradiance that is significantly higher than QFS-40 lamps in the same tester.
To read more about Q-Lab and to find more articles like this, please visit Q-Lab Blog.
In Xenon and UV fluorescent accelerated weathering testing, an irradiance setpoint value is incomplete information without reference to the wavelength or wavelength range it represents. There are two classes of irradiance setpoints.
Narrowband irradiance setpoints include 340 nm and 420 nm, and represent a 1 nm wide bandpass, centered on the single wavelength value indicated (i.e. ½ nm on either side of 340 nm, for example). Narrowband irradiances use units of “Watts per square meter per nanometer.” This can be written as either W/(m2∙nm), W/m2/nm, or W∙m-2∙nm-1.
Wideband irradiance setpoints (usually “TUV” or “total UV”) are an integration of the irradiance from all wavelengths between two endpoints, usually 300-400 nm (accelerated laboratory) or 295-385 nm (outdoor). As a result, wideband irradiance values are generally much larger than narrowband irradiance values. Wideband irradiance is measured in “Watts per square meter,” written as W/m2 or W∙m-2.
The graph below is a spectral power distribution (SPD), which presents irradiance as a function of wavelength. This SPD shows that, for this particular light source, one could describe the irradiance either as having a narrowband irradiance of 0.35 W/m2/nm @ 340 nm, OR as a wideband irradiance of 40 W/m2 from 300-400 nm (TUV).
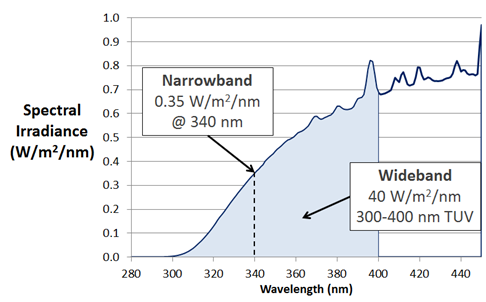
To read more about Q-Lab and to find more articles like this, please visit Q-Lab Blog.
Weathering and lightfastness test standards typically specify an irradiance level as both a magnitude and the wavelength (or wavelength range) where it is controlled. Irradiance in fluorescent UV and xenon arc weathering testers can be controlled using narrowband or wideband setpoints.
The selection of a narrowband control point in a QUV fluorescent UV tester is determined by the UV lamp type in use. For a Q-SUN xenon arc weathering tester, we suggest control using a wavelength or wavelength region in which the test specimen is sensitive. If the user is primarily concerned with color change, then a 420 nm control point is often used. If the primary area of concern is another type of physical property change, gloss loss for example, then a 340 nm control point is frequently used. A wideband TUV control point (300-400 nm) can be viewed as a compromise between the two narrowband (340 nm & 420 nm) control points, as it uses the total irradiance over the range 300 400 nm as its setpoint.
Selection of optical filters in a xenon arc tester also usually parallels this selection of irradiance control point. Typically, users testing with daylight optical filters use a 340 nm control point, while users of window glass optical filters generally use 420 nm control point. The available and most common selections for each lamp or filter type are presented in Table 1.
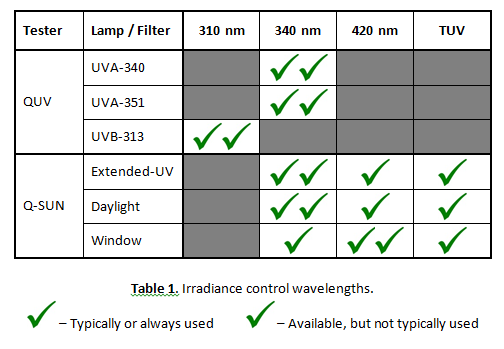
To read more about Q-Lab and to find more articles like this, please visit Q-Lab Blog.
In accelerated weathering testing, water is often the most difficult factor to accelerate. You cannot make water sit on a panel “faster” in a tester than in the real world. Since many materials outdoors will be wet for 8 to 12 hours a day, an accelerated test in many cases needs to simulate the same deep penetration of water into the material in order to correlate to real world conditions – and this means it has to be wet for a long time.
One way we can accelerate the effects of water is by increasing the temperature of the water. As the temperature increases, the air can hold more water vapor, which allows for increased water absorption into materials. Since condensation is formed from hot water vapor, the temperature of the water is easily controlled and the chamber can reach temperatures up to 60 °C. In contrast, it is difficult to run a water spray step in a Xenon Arc or Fluorescent UV tester while simultaneously maintaining high specimen temperatures, which is why water uptake is more difficult with spray than condensation.
But How “Wet” is a Condensation Step?
It’s hard to really appreciate how wet a condensation step is because it’s less obvious than looking at water spray. Figure 1 shows a set of seven pictures demonstrating how wet the first hour of a condensation step is.
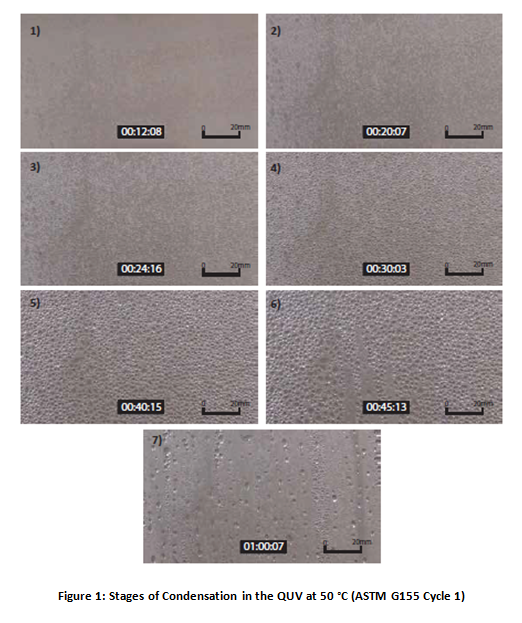
Once all of the initial droplets have run off the specimen, the cycle repeats with the formation of small droplets, those droplets getting larger, and those large droplets running off of the specimen. At any time 20 minutes or longer into the condensation cycle, the specimens are covered in water, and over the course of four hours, condensation is continually forming and dripping off of the specimens.
Most people would expect that weathering test specimens in a QUV condensation step are exposed to only a small amount of water. In reality, over four hours, a condensation step not only provides almost continuous exposure to aqueous water, but also elevates the temperature of the saturated air, exposing a specimen to a higher amount of water vapor. Unless you’re testing a thick, insulated material, hot condensation in a QUV tester is the best way to accelerate water uptake in a weathering test.
To read more about Q-Lab and to find more articles like this, please visit Q-Lab Blog.
The irradiance uniformity of the QUV accelerated weathering tester is excellent - greater than 90% over the specimen exposure area.
The irradiance uniformity can drop on the edge of the tester due to physical and geometric limitations that apply to all fluorescent UV testers. For this reason, Q-Lab suggests regular specimen reposition. This practice improves water spray and temperature uniformity in accelerated weathering and corrosion testers as well.
With proper installation and specimen mounting, the temperature uniformity in the QUV is also very good. It is very important, however, that you avoid leaving any gaps on the ends or between specimens. These gaps cause air to rush out of the chamber, which causes cooling on adjacent specimens and causes hot spots in other locations.
To read more about Q-Lab and to find more articles like this, please visit Q-Lab Blog.
International standards for operating weathering test apparatuses using Fluorescent UV and Xenon Arc lamps often include requirements for relative spectral power distributions (SPD’s) of the light sources. These SPD’s define ranges for what percentages of a given light source’s irradiance fall within a specified bandpass, e.g. 290-320 nm or 360-400 nm.
Important sets of SPD reference tables are provided in both ASTM and ISO standards. Fluorescent UV spectral tables are provided in ASTM G154 and ISO 4892-3, while xenon arc requirements are found in ASTM G155 and ISO 4892-2. These tables are defined for three different general classifications of lamps and filters: Daylight (outdoor sunlight), Window (behind glass), and Extended UV (UVB-313).
Q-Lab’s UVA-340, UVA-351, and UVB-313EL lamps all meet the specifications of both ASTM G154 and ISO 4892-3 for Daylight, Window, and Extended UV.
The following Q-Lab UV filters used in Q-SUN weathering testers meet the spectral requirements specified in ASTM G155 and ISO 4892-2. The latter standard does not include a specification for Extended-UV.
Table 1 (Daylight filters): Daylight-B/B, Daylight-Q, Daylight-F
Table 2 (Window glass filters): Window-B/SL, Window-Q, Window-IR
Table 3 (Extended-UV filters): Extended UV-Q/B
The only Q-Lab standard optical filters that fall outside of these SPD requirements are the Extended UV-Quartz and the Window-SF5 filters. The Extended UV-Quartz filter is required only in a few specialty aerospace standards, while the Window-SF5 filter is used only in automotive standards specifying glass with higher cut-on wavelengths than architectural glass.
To read more about Q-Lab and to find more articles like this, please visit Q-Lab Blog.
The water pan in a QUV tester is made from stainless steel, and in most cases does not experience corrosion. To deal with those rare cases where a QUV water pan does corrode, Q-Lab offers a “Super Alloy” QUV water pan that is more corrosion-resistant than stainless steel.
This Super Alloy water pan is not intended for cases where the observed corrosion or oxidation is actually only non-corrosion debris, as in the photo below. This buildup of precipitated minerals over time may occur when tap water is used in a QUV SE or Basic testers (DI water is required for Spray models). Although tap water is acceptable for use in a non-spray QUV, its use does requires more frequent cleaning of the water pan. If you see debris buildup like this in your QUV, you may have “hard water” and should consider the use of reverse osmosis/deinoized (RO/DI) purified water with your QUV.
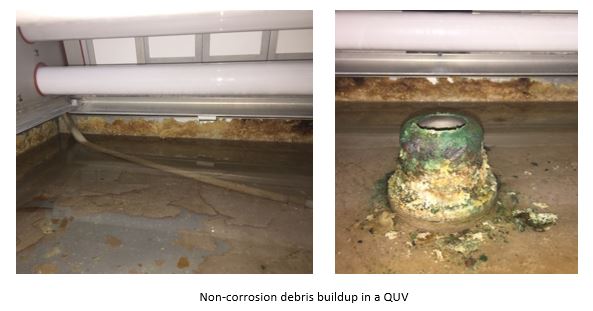
However, in some cases, actual corrosion of the stainless steel water pan is observed, as in the photo below. Replacing your stainless steel QUV water pan with a Super Alloy water pan is appropriate to correct this problem. Furthermore, if corrosion like this is observed in one QUV, a Super Alloy water pan should be installed in all other QUV’s located in the same laboratory as the corroded QUV.
To read more about Q-Lab and to find more articles like this, please visit Q-Lab Blog.
Legionella is a group of bacteria that can cause a pneumonia-type illness called Legionnaires' disease and a mild flu-like illness called Pontiac fever. Legionella can grow in drain traps, water pans, reservoirs, and commercial and industrial cooling towers. Although Q-Lab’s QUV and QCT testers have warm, wet conditions that could be conducive to microorganism growth,
there have been zero reported cases of Legionnaire’s disease related to QUV and QCT usage over 45+ years and millions of hours of field operation. This is largely because the QUV and QCT are usually run at temperatures that kill the Legionella bacteria. The best means of prevention is perform basic maintenance that avoids water conditions that allow microorganisms to grow to high levels. This includes:
- Draining water from unused testers
- Performing regular maintenance and cleaning of cooling towers and evaporative condensers
- Disinfecting with a mild bleach solution
- Maintaining water heaters at 60 °C (140 °F)
- Avoiding conditions that allow water to stagnate by protecting water tanks from sunlight, and draining and flushing unused water lines
- Keeping all water lines short and maintaining flow
There have been zero reported cases of Legionnaire’s disease related to QUV and QCT usage over 45+ years and millions of hours of field operation. Properly maintaining Q-Lab testers is the best way to reduce the already minuscule risk of Legionella.
To read more about Q-Lab and to find more articles like this, please visit Q-Lab Blog.
QUV and Q-SUN accelerated weathering testers require the use of special calibration radiometers. The CR10 and UC10 are used for fluorescent UV lamps and the CR20 and UC20 are used for xenon lamps. These NIST-traceable devices ensure that the irradiance delivered to test specimens equals the irradiance called for in the user’s test method. Q-Lab’s lamps must be calibrated specifically with this radiometry equipment because of spectral mismatch between different UV fluorescent lamps or optical filters. Spectral mismatch is the effective difference in reading observed from an irradiance sensor when using a different spectrum than was used for calibration.
Q-Lab’s on-board and calibration irradiance sensors work using a photodiode, a semiconductor that converts absorbed photons into an electrical current. Since the photodiodes used in irradiance sensors only measure the intensity of light, but not the wavelength of light, filtering is used to make narrowband (310 nm, 340 nm, 420 nm), or wideband (TUV, 300-400 nm) irradiance measurements. If an on-board sensor is calibrated with a particular light spectrum, some error will be introduced when trying to measure irradiance using a different light spectrum.
For example, in a QUV, if you were to try and measure the irradiance of a UVB-313 lamp using a radiometer calibrated for use with a UVA-340 lamp, you would get an erroneous reading. A similar error would occur in a Q-SUN if trying to measure the irradiance at 340 nm with a Daylight-F filter using a radiometer calibrated for Window-Q. This is why it’s important to use the correct setting and device when calibrating a QUV or Q-SUN accelerated weathering tester.
To read more about Q-Lab and to find more articles like this, please visit Q-Lab Blog.