Overview and Problem Statement
A manufacturer of adhesives and fillers was looking for a way to better simulate yellowing failures of their products that they have seen in the field. Their products are used in the bonding, filling, and repairing of stone, concrete, ceramic, and coatings for the automotive, architectural, and other industries. Key failure modes are color fading, gloss loss, mechanical strength loss, peeling, and cracking. This was not so much a warranty claim issue, as it was an opportunity to grow their market share in harsh geographic environments (especially the Middle East). Their technology, used outdoors in all types of climates around the world, is based on polyester and polyurethane epoxy resins.
Testing Description and Results
This manufacturer came to Q-Lab for help. With Q-Lab’s assistance, they focused on performing comparison trials in QUV and in Q-SUN xenon arc test chambers in order to find out which technology correlated better to their field failures. Testing was performed for 500 hours according to ISO 4892-2 (xenon) and -3 (fluorescent UV). In both cases, Cycle 1 of the mentioned standards was chosen.
- QUV: A light and condensation cycle was run with UVA-340 lamps. The light step is 8h, irradiance setpoint 0.76 W/m2/nm @340 nm, 60°C; the condensation step is 4 h at 50°C
- Q-SUN: An alternating light / light+spray cycle was performed using Daylight-Q filters. The cycle consisted of 102 mins light at 60 W/m2 TUV (300-400 nm), 65°C Black Standard (IBP) temperature, chamber temperature 38°C, RH 50%; followed by 18 mins of light plus water spray.
After 500 h, most test specimens showed substantial changes in both QUV and Q-SUN testing, as shown below in Figures 2-4.
In more detail, epoxy resin results are shown in Fig. 2 for several transparent coatings, as well as a colored specimen. Fluorescent UV testing generally produced more severe yellowing and color fading than xenon testing, as well as cracking/crystallization for certain specimens that was not observed in xenon testing. The UV fluorescent test results most closely represented field failures.
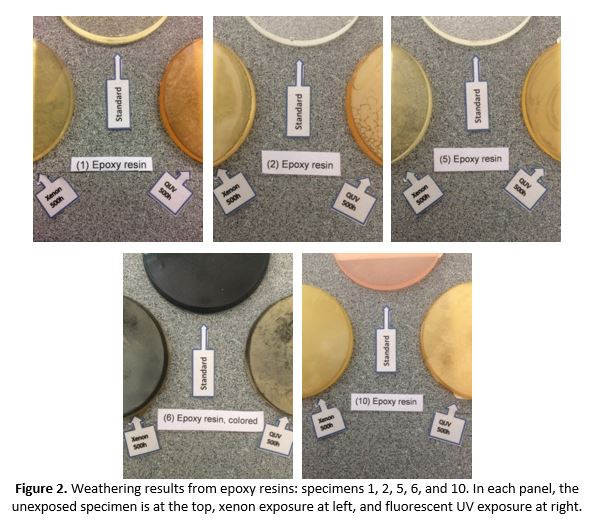
Acrylate test results are presented in Fig. 3. The polymethacrylate (3) and epoxyacrylates (4), (7) show comparable aging yellowing results between the UV fluorescent and xenon test methods.
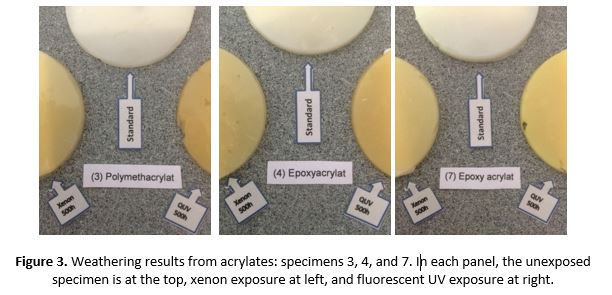
Polyurethane (8) and polyester (9) results are presented in Fig. 4. As with the epoxy resins, fluorescent UV testing resulted in slightly more yellowing than the xenon testing, and most closely mimicked field failures.
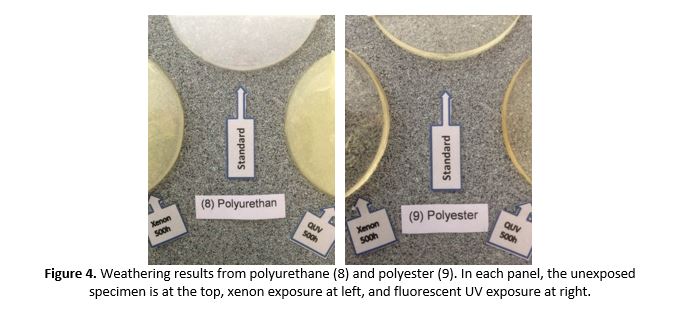
Benefits of Testing
Based upon these test results, this manufacturer purchased a QUV tester for internal R&D use, to help reformulate their products (especially their epoxies). The QUV has provided them with a repeatable method for performance testing with good correlation to real-world conditions, something they have not had previously. This allows them to compare their new products with previous formulations, as well as those from competitors. While quantified business results have not been shared with Q-Lab, it has been confirmed that the QUV purchase has paid for itself in a very short timeframe, and has helped this company to substantially increase its market share in certain targeted geographic regions.